Warehouse receiving operations are a critical part in maintaining the integrity of inventory systems and ensuring the availability of products for customers. Without an effective receiving system, items fall through the cracks, are not counted, do not receive adequate inspection, and fail to provide evidence of problems with vendors that affect profitability.
Why do we like to call Receiving the “Lynchpin Process” of your warehouse?
Receiving is placed in front of all the other processes and if it’s not running at maximum efficiency, it adversely impacts the entire shipping and receiving process workflow and all the downstream processes. This causes jamming up the dock, mislabeling items for putaway, and paying trucks for idle time waiting for a bay to open.
How do the smoothest running facilities maintain a solid shipping and receiving process workflow?
It starts with a great plan, which leads to an optimal dock design, as outlined in our “Warehouse Efficiency Tips”. A key aspect of designing your space to optimize Receiving is making the most of the layout and number of bays you have in your facility.
A comprehensive management program must be included in any business system to eliminate waste and inefficiencies that can occur at this level of operation. Success in the supply chain at the level of warehouse management can have a direct effect on the profitability of the business as a whole.
Today's Warehouse Receiving Systems
Receiving operations involve the transfer of ownership of goods, which by its nature involves financial responsibility. Ensuring that the documentation is accurate, correct and smoothly and efficient allows the material to be made available to the customer as soon as possible. An accurate reporting of what is received has a direct effect on the accounting and payout for goods.
Inaccuracies in counting or failure to report damaged or missing items means the business will be paying for goods they did not receive, which affects the bottom line on an ongoing basis. Finding ways to improve the shipping and receiving process workflow makes the process accurate, foolproof and easy improves profitability for companies in a practical way.
Free Bonus: Download the Receiving Revolution White Paper and reduce receiving errors and inefficiencies. |
What’s the result of all those wasted footsteps in receiving? Time is wasted, and with labor at a premium, it not only cost money, but reduces your productivity. And what’s the solution? Since the footsteps come from walking to a printer, you can eliminate most of them by putting your printer on wheels – and taking it to the work. The concept is simple. Putting a powerful, lightweight lithium battery pack on a cart designed not only to carry your label printer but the entire workstation including a laptop, monitor, scanner, or other peripherals not only improves your productivity, but does it in a way that reduces fatigue and improves employee morale. When a facility updates their Receiving process by making the printers mobile, the impact on your “dock-to-stock” metrics is instantaneous. As many managers have discovered, receiving productivity can double quickly after deploying the carts.
Improving Warehouse Receiving Efficiency
Essentially, the same warehouse decisions are made today as they have been since the beginning of large-scale industrial operations, that is, location, personnel, equipment, and schedule.
Though the technology has changed significantly, these primary actions are required in every circumstance. Implementing simple systems such as dock scheduling, which requires shippers to notify the receiving department 24 hours in advance of a delivery can help managers of these operations to ensure that the appropriate shipping and receiving process workflows are available at the time they are needed.
The scheduling operation can make a radical improvement in the ability to manage incoming materials and ensure that accurate inspection, labeling, and counts are produced. Another strategy, cross-docking, immediately sends materials to another dock for shipment, when storing the items are not required. This method provides another way to implement efficient use of dock and storage space for better efficiency.
Proper Labeling of Received Goods
Labeling of received materials has changed dramatically in recent years. Computerization, bar-coding, radio-frequency ID scanners and automated pallet management and storage systems have made warehouse receiving more complex and more accurate than ever before.
However, these systems also require more training of personnel to ensure that they are implemented correctly to maximize the benefits.
Your Receiving Process Flows Downstream to Other Processes
Accountability is one of the critical aspects of warehouse receiving operations. Each worker must record his or her actions in the context of the overall operations. In this way, problems of miscounts, defective shipments and incomplete deliveries are not overlooked during a hectic delivery day.
Changing technology often necessitates a change in the process, in by whom, where, and how long materials are handled before they can pass through the system and be available as regular inventory. Exceptions to the standard process should be eliminated as much as possible to reduce both costs and errors.
Your Receiving process – and the flow downstream to other processes - will all be greatly impacted by the design of the building you are in! But design can only facilitate a process, not change one that is already not performing optimally.
How do you improve your warehouse Receiving process if it’s not performing to expectations?
It starts with understanding where the challenges are. An app like MotionMeter can get you started by measuring the wasted footsteps that are common on most receiving docks. It’s common for process “measurement” to omit elements not directly listed as part of the movements involved in a process.
Does your Receiving process include “walk from receiving dock to office and print labels for incoming pallet(s)”?
Probably not. A measurement tool like MotionMeter gives you an easy way to document those steps along with the rest of your process – for Receiving AND other processes too!
Inspecting incoming Product at the Beginning of the Receiving Process
Inspection is as important to incoming items as it is to outgoing items. It is here, at the beginning of the shipping and receiving process workflow, that problems with vendors, shippers, and other handlers can be found.
Because items can be immediately assessed at this point, sufficient time and manpower should be in place for inspection to provide accurate inventory data and report any problems with the vendor or shipper. In this way, inadequate packaging or delays in shipping can be evaluated and addressed, as needed.
Establish an Accurate Replenishment Process
Warehouse receiving processes must all be connected to an accurate replenishment process that ensures re-order of items at least 2 to 4 weeks in advance of being needed.
An efficient warehouse system will eliminate miscounts and warehousing of defective items that disrupt the ability to keep a sufficient amount of suitable materials on hand. In this way, your warehouse receiving system works together with your purchasing department to increase the efficient operation of your business.
Ensuring the best shipping and receiving process workflow requires both regular examination of operations to find problem areas, as well as ongoing effort to implement logistics solutions that increase data collection and improve physical systems. CTA “Operations Director Guide to Doubling Warehouse Receiving Productivity”
The hundreds of Top 500 Retailer and 3PLs that now use “mobile powered receiving station” all agree that “Mobile Printing Solves a Problem We Didn’t Know We Had!”. Many of them with fleets of carts in multiple facilities started with two or three to test the waters in Receiving and quickly found the ROI worked within six months.
Compiling the Right Metrics
Designing and implementing the most effective systems relies on the collection of the right metrics. These generally include:
- Dock to stock time - the total time needed to move materials through the system to usability
- Receiving error reporting - systems should be in place to double check the system through label scans to alert to errors during the warehousing process
- Dock utilization - tracking of the utilization of dock doors, as well as space to ensure maximum efficiency
- Supplier shipping problems - recording errors by the shipper, such as incorrect qualities, the wrong product or paperwork mistakes, so shippers can be alerted to problems
The Productivity and the Versatility ROI.
How does the math work?
When you have your printer moving with you while you process an incoming shipment, it means the team never leaves the dock to get labels, the labels are printed on demand so there are fewer mistakes (and less waste), and the speed of the processing means product moves of the dock and into storage faster, ending the wait for trucks idling in the yard. This example shows both the productivity and the versatility that comes with introducing mobile power with modern label printers on a cart:
But how do you know it will make a difference in YOUR facility?
Now that you know receiving may have more opportunities for improvement than you previously considered, you might be asking “Just HOW MANY steps do we take getting to our printer?” and may have already measured it. And you may have already taken other steps that improve how to streamline material handling during receiving too. But after all that can a mobile powered cart really change your outcomes that much? If you do know your step counts, then you can calculate exactly how much you can save and how long it would take to get the return on investment that justifies it:
The Next Level of Warehouse Workflow is Cross-Docking.
Once you’ve optimized receiving and get used to seeing those wide-open spaces, you’re better able to utilize the space for other advanced processes like cross-docking. Cross-docking is the process that you can use when you have a high-volume, fast-moving product that needs to go out as soon as it comes into your warehouse and involves product going directly from receiving to shipping without ever being put away into inventory or in the picking aisles. They key is getting the paperwork done right to minimize mistakes and maximize the speed.
Increase productivity and wellbeing of the Warehouse Team
One additional benefit not always included in process analytics is the fatigue aspect and the ergonomic impact on workers. Eliminating excess footsteps makes financial sense and is always a part of the process improvement work, but it also reduces fatigue which means workers not only keep their productivity levels more consistent at the end of the day but also reduces their down time for illness or injury. While fatigue itself is not something you would normally measure in a warehouse, removing sources of it from the workspace will make a difference, which the fast-paced nature of the pandemic spike has proven would grow in importance regarding best practices in managing human resources.
As a “lynchpin process” receiving has far more impact on the productivity of your warehouse than is commonly understood. By implementing the relatively small investment of a Mobile Warehouse Receiving Cart you will see the immediate – and measurable – benefits in a noticeably short time. What are the key metrics you measure in your shipping and receiving process workflow?
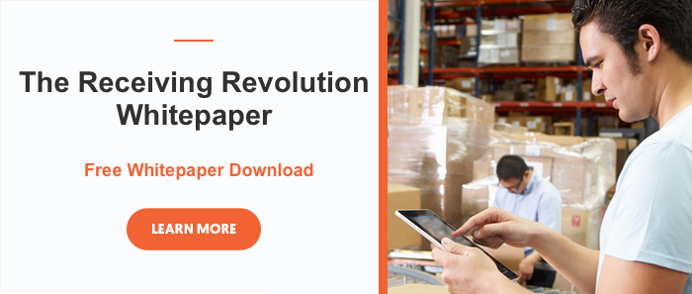