While there is generally NOT any disagreement about the need for quality control, there are definitely different levels of appreciation for it and commitment to it. No manufacturer would want to admit to not having a quality control process, and we assume that it would be rare to find any that don’t. However, there are a lot of myths about the topic which permeate perhaps because they work as an excuse for not doing things to the level the business should be – or is capable of. Change is hard, but the myths make it harder. Here are five of them we dispel here today.
Quality Control – What is It?
If we want to go with a sterile dictionary definition, we could define it as a process that “consists of activities employed in detection and measurement of the variability in the characteristics of output attributable to the production system, and includes corrective responses.” (Thanks Business Dictionary!)
Using a more colloquial description, it’s the steps you take every day, in a structured manner, that ensure that your products leave the factory fulfilling the promise you made about them. And then finding more ways to improve upon it.
Here are five things it is NOT:
1. Quality Control is Just a Fad
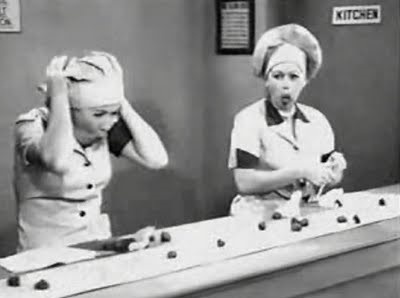
Dismissing efforts to make an improvement in this area as a “fad” is generally a lazy management approach to avoiding a problem.
2. We Already Have Great Quality, Our Customers Always Say So
It’s entirely possible you are part of a supply chain where your customer is already certified to do quality inspections of your work. But do all of your customers have that ability? And do they all have the same certification? For a new customer who does not, how do you verify for them your quality records - by having them take another customer’s word for it – who might also be their competitor?
And…who are you to say you are on top of the latest innovations in QC if you are not certified and plugged into the knowledge base of an accredited certification body?
Don’t fool yourself. Get your own management system in place get the certifications you need and demonstrate genuine discipline in this space. An accredited certification has something new for everyone to learn.
3. Requires Too Much Documentation and Paperwork
There seems to be a running theme in all of these “myths” about quality control. A lot of them seem to be a call to complacency. In this case, it is easy to believe this since no one likes to see more paper flying around in an industry that is trying to go paperless. But if we look at the most popular management system in the world, ISO 9001, we get all the transparency, structure and trust needed for the business, its employees and its customers from only six documented procedures. Instead of focusing on the documents, focus on the bottom-line value you should be getting first. If you are investing in things based on the ROI they give your organization and the value to your customers, then the document count should not be your focus. Solve the quality issue first, then deal with the documents as a separate issue, just as you would approach any other effort to go paperless.
4. It Adds Unnecessary Costs to My Business
If you were going to go on vacation in a week but found a leaky pipe in the wall of your bathroom, what would you do? Would you complain the fix is too expensive and deal with it when you come back, or would you see far ahead enough to know that replacing your drywall and carpet a month later will cost you a lot more?
The cost of implementing a new QC process might seem expensive. It could include new personnel, training, certification, process re-engineering and perhaps even some new equipment. It may seem expensive because all of those costs are known to you up front, while the costs of NOT implementing a QC process needs to be calculated, research and/or derived. The cost of not doing it could include:
- Scrapped products
- Downtime on the floor
- Lost customers
- Lost sales
Some of these are probably already measured and easy to measure, but if you are not aware of how your quality issues affect lost sales or customers, then you won’t be in a position to judge if the implementation cost is truly “unnecessary.”
5. There are no Legal Requirements For This in My Industry, So Why Bother?
One of the keywords missing from this myth is “Yet”. Because even if your belief that you have no regulatory obligation to step it up in the QC department, you are also assuming that you will never have to, and that is very shortsighted. A good QC process provides a practical, systematic methodology for business to achieve the results they and their customers need. Getting an internationally recognized accreditation is also a great marketing and sales tool, especially if you have competitors who think like this too and aren’t bothering to implement anything formal. And introducing a management system like QC has additional benefits that will grow over time as well. The transparency from documenting your methods, measurements and results:
- Provide a rich resource for future product improvements
- Can be re-purposed into training material
- Will give you a proactive stance to deal with any potential regulatory or legal changes
- Generate financial benefits derived from the preventative practices put in place with your QC process
“Myth” is a Synonym for “Excuse”
With Quality Control and Quality Assurance now expanding their presence into every part of the production process, sitting on the fence about taking your efforts up a notch is simply a way to ensure you will be creating bigger problems for your own organization down the road. For small manufacturers, getting started is sometimes the hardest part, especially if you have not previously implemented this kind of process before (See our previous article on “An Introduction to Quality Control in Manufacturing”).
It does pay to get outside help, but only to get yourself setup. This is a core competency that is at the heart of your relationship with your customers. Relying on a 3rd party to actively manage your quality control is not recommended. It’s best to invest up front and get the expertise but then ensure you own this process internally.